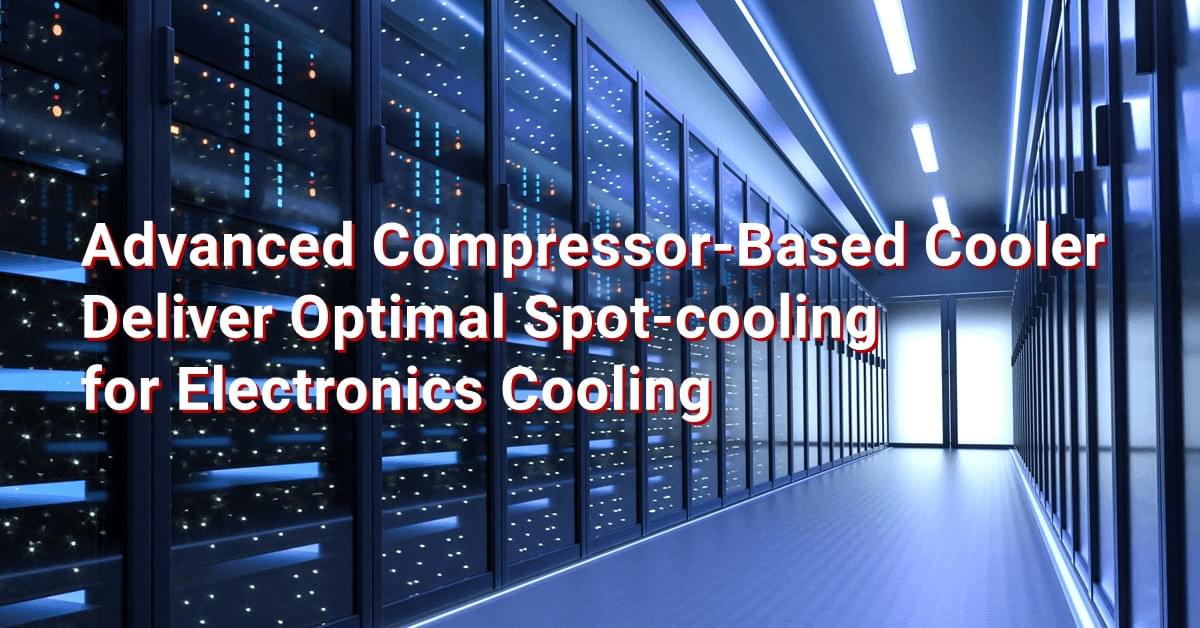
1. INTRODUCTION:
All electronic equipment requires some form of cooling to prevent overheating and failure. In practice, electronic equipment is usually placed in an air-conditioned office with a simple fan blowing through it to prevent overheating. However, a simple fan cannot provide sufficient cooling. This is especially the case when electronics are used in mobile or remote areas, far from the power grid, where fans or traditional air conditioners do not work.
Electronic devices are often placed in an enclosure to protect them from rain and mud. The electronic equipment inside does need a cooling system to ensure that the enclosure does not overheat and cause shutdown or permanent damage. When ambient temperatures are high, active cooling can provide enough cooling to cool the electronic equipment.
Until 2008, most small refrigeration systems used for cooling electronics and precision instruments were based on thermoelectric technology. Unfortunately, thermoelectric systems consume 4 to 6 times more electricity than equivalent vapor compression systems, making them very expensive to operate. In addition, thermoelectric modules are made of delicate semiconductor materials and require large and heavy structures. Thermoelectric modules are large, consume high amounts of electricity, and have a much lower energy efficiency ratio than compressor cooling systems.
Therefore, the only cooling systems for electronics enclosure cooling are large, heavy, and inefficient thermoelectric systems.
In 2010, RIGID developed and put into production a miniature refrigeration compressor (as shown in Figure 1), which is 10 times smaller and 10 times lighter than a conventional AC compressor of equivalent capacity. The following year, RIGID succeeded in developing a micro dc aircon for electronic cooling applications. The world's smallest and lightest micro compressor system was developed and put into production by RIGID Technology using this advanced micro compressor. This dc aircon unit (as shown in Figure 2) is widely used in small confined space cooling (<2m³).
Figure 1, RIGID miniature dc compressor.
Figure 2, RIGID Micro DC Aircon.
By 2020, more than 10,000 micro aircon units have been shipped to the United States and European and Middle Eastern countries for use in hostile, dirty, and harsh local environments. This is the benefit of the high efficiency of the RIGID micro aircon units.
Today, RIGID has a lineup of miniature cooling systems (as shown in Figure 3) that are highly reliable and the micro vapor compression technology employed is used to protect mission-critical computing and communications systems. A new vapor compression technology is being used to protect mission-critical computing and communications systems for the first time.
Over 10000 of these systems have been in use on electronics and lithium batteries for over 2 years. With a maintenance-free design and an over 100,000-hour mean time between failures, RIGID miniature vapor compression cooling systems demonstrate reliability and effectiveness.
In a preliminary evaluation, RIGID compared the basic size, weight and cooling capacity of both miniature compressor system and TE cooler, as well as the rated characteristic conditions. In the comparison tests, the internal thermal load has been changing and the power consumed to maintain the internal temperature of the electronics was measured. The data in Table 1 shows that the micro aircon unit DV3220E-AC has a smaller footprint and weighs less than the TE cooler. The DV3220E-AC provides a cooling capacity of 550W, while the TE cooler has a cooling capacity of just 303W. The results are clear: the miniature compressor system has almost twice the cooling capacity of the TE cooler.
Figure 3, RIGID miniature cooling systems.
2. Transit Case Cooling Options
Miniature compressor cooling and thermoelectric cooling are the only two technology options for achieving refrigeration of transport cases and other precision electronic instruments. Given the success of Micro DC Aircon products in field operations, RIGID miniature cooling units are the best choice. Now in order for manufacturers to develop the optimal cooling solution for their applications, they need to understand how these technologies differ in performance.
To fairly evaluate the size, weight, cooling capacity, efficiency, and relative cost of both micro compressor and thermoelectric technologies, RIGID conducted thermal evaluation testing of the 24V DC Micro DC Aircon, model number DV3220E-AC, and TE cooler. The DV3220E-AC, shown in Figure 4, is a compact, rugged vapor compression air conditioner rated at 550W (1875Btu) for air-cooled transport electronics enclosures. A competing TE cooler with similar ratings and rugged military performance was selected for comparison. This TE cooler is rated at 1500 Btu (440W).
Figure 4, RIGID Micro DC Aircon Drawing.
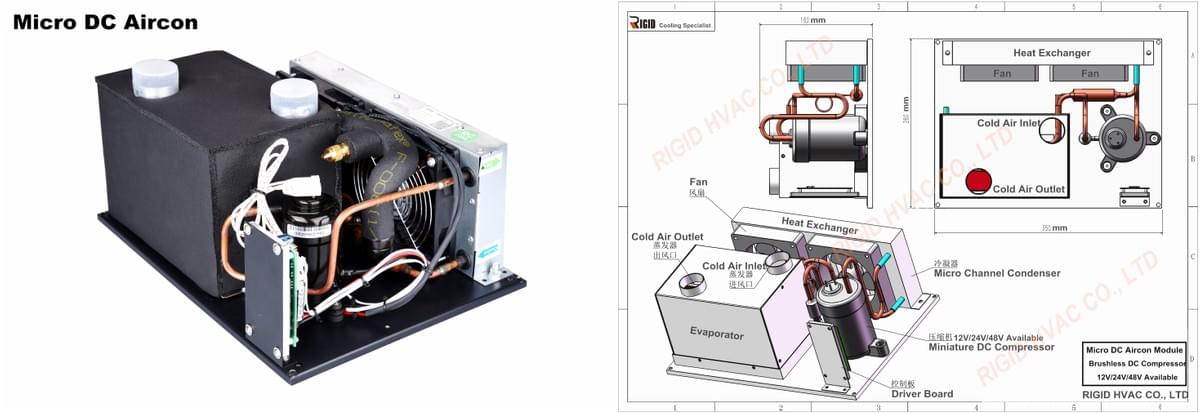
Rigid's evaluation methodology examined each product under the same environmental conditions, using the same shipping box installation and thermal chamber. A series of performance data was generated using a common electric heat source to determine cooling capacity and power consumption at different ambient and internal transport temperatures. The results of these tests are listed below, and we can clearly see the limitations of the thermoelectric system and the high energy efficiency of RIGID's micro air conditioning unit products. For the latter analysis, RIGID assumed a military mobile communication system mission scenario for electronics cooling applications.
3. Baseline Performance Comparison
In a preliminary evaluation, RIGID compared the basic size, weight and cooling capacity of both miniature compressor system and TE cooler, as well as the rated characteristic conditions. In the comparison tests, the internal thermal load has been changing and the power consumed to maintain the internal temperature of the electronics was measured. The data in Table 1 shows that the micro aircon unit DV3220E-AC has a smaller footprint and weighs less than the TE cooler. The DV3220E-AC provides a cooling capacity of 550W, while the TE cooler has a cooling capacity of just 303W. The results are clear: the miniature compressor system has almost twice the cooling capacity of the TE cooler.
Table 1, *Test Conditions 120°F Ambient/120° Internal
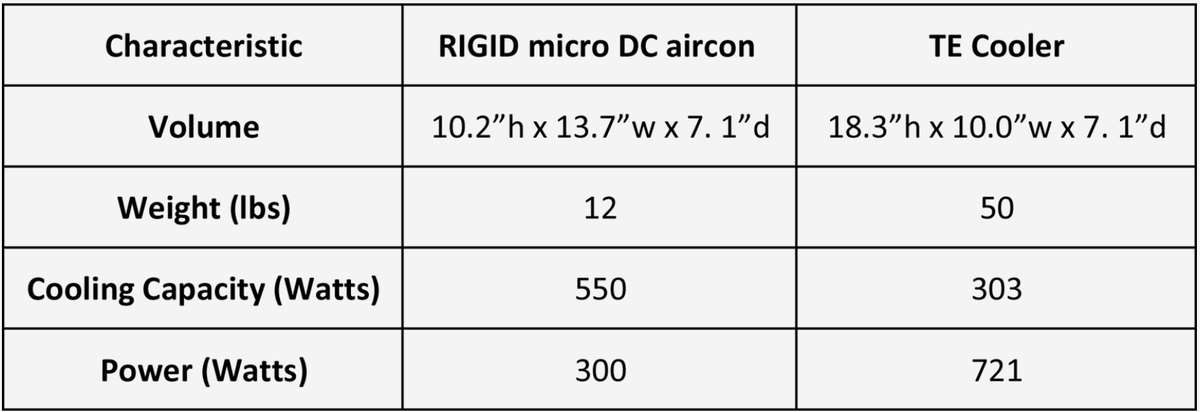
In addition, it consumed much less energy than 550 Watts to cool the thermal load, 303 Watts versus 550 Watts, respectively. In comparison to thermoelectric technology, vapor compression has significant advantages.
To fairly evaluate the characteristics of micro-compressor systems and thermoelectric systems, and to select the optimal cooling solution, RIGID has normalized the characteristics required for the required cooling capacity in the application in comparative tests.Thus, as an example, we normalize the characteristics per 100 W of cooling capacity and evaluate their economic efficiency in a task scenario of cooling electronic devices at a specific power rating. Refer to Table 2 for data showing the results of the normalized comparison. RIGID Vapor compression systems are 3 times smaller, more than 4 times efficient and 5 times lighter than thermoelectric coolers.
Table 2, Vapor Compression cooling is 3 times lighter, 4 times more efficient, and 5 times lighter than thermoelectric.
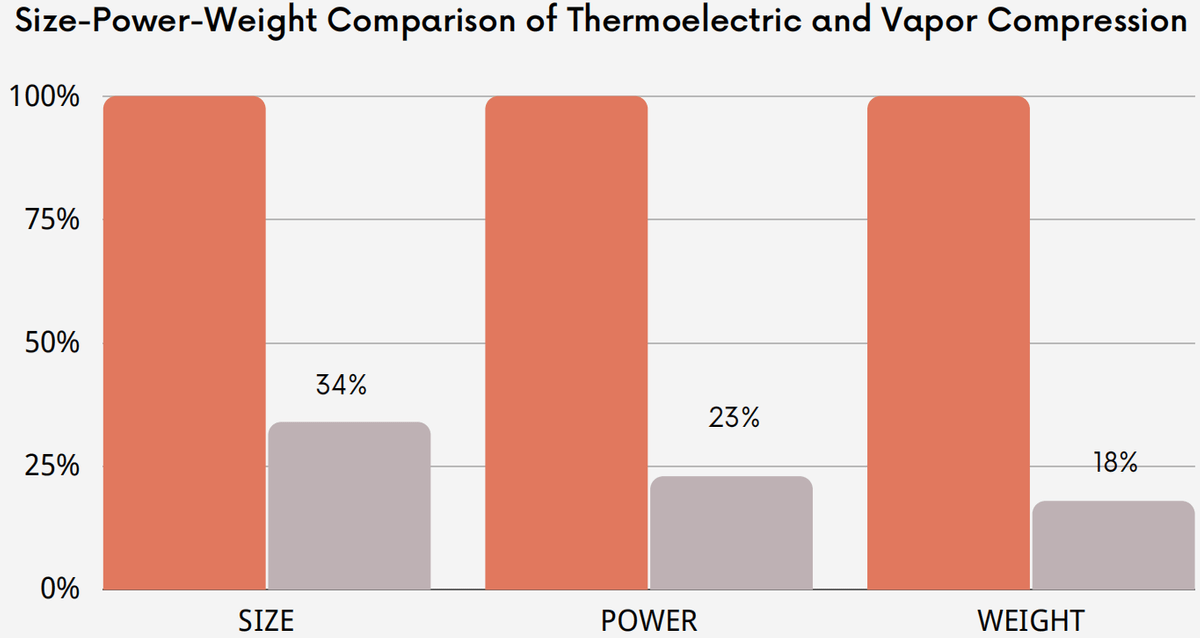
If you have a need for a micro cooling system for your precision instrumentation, or electronic equipment cooling, do not hesitate to contact info@rigidhvac.com
4. Life Cycle Cost Advantage
Probably the biggest misconception about the two technologies, miniature compressor cooling and thermoelectric cooling, is that TE coolers have an advantage in terms of operating costs. However, we must also consider that TE cooler technology is inherently 6 times less efficient than compressor-cooled systems. System integrators should also consider the greater power requirements of TE coolers. Moreover, the energy efficiency ratio of TE coolers is only 1/3 that of compressor systems. Therefore, the total cost of a compressor system is lower in terms of operating the system over its entire life cycle.
In addition, in terms of operating noise, RIGID has successfully developed a twin-cylinder mini-compressor with a noise level of 36 dB, which is excellent in the industry. Moreover, RIGID's twin-cylinder compressors are able to withstand high temperatures up to 55°C. Currently, they are widely used in outdoor communication equipment base stations like telectom base in tropical areas. Figure as shown in Table 3, more than twice as many TE cooling units are required to meet the requirements of the task. The TE cooling unit is much heavier and larger in size compared to the RIGID compressor mini-cooling system. At the same time, more power is consumed than in a compressor system. So, at first, users may mistakenly believe that the initial cost of a compressor system is higher.
Table 3, Field Command Post with 6KW Cooling Requirement.
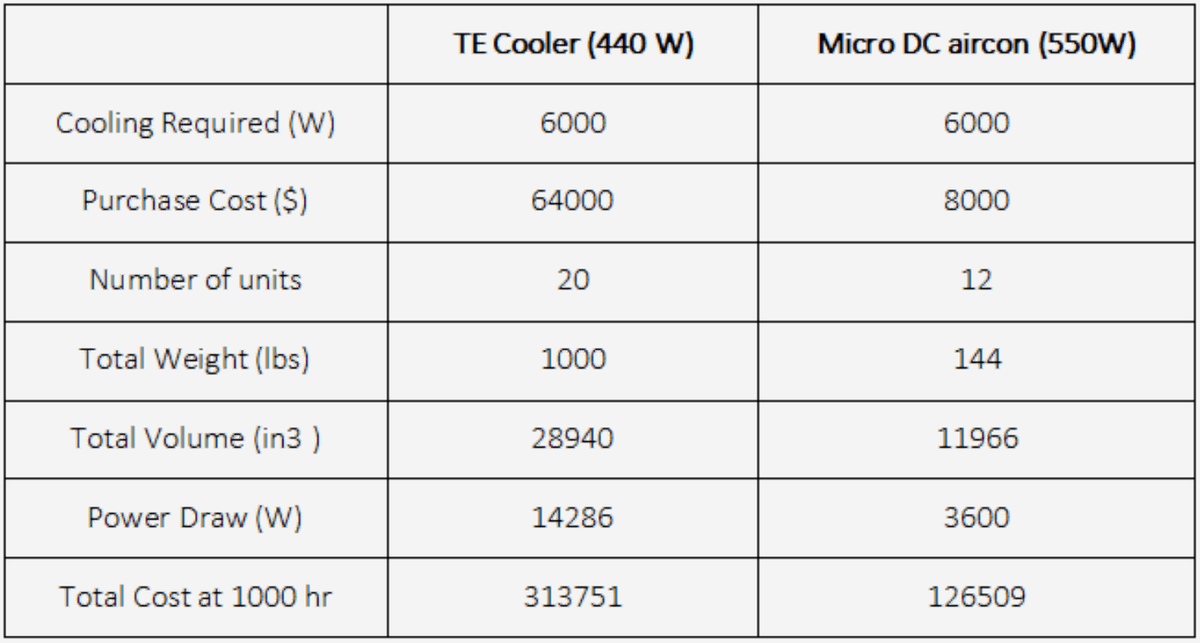
However, when considering the need for more TE coolers in the same application and the increased cost of electricity to operate these units during a mission, the significant advantages of a compressor micro-cooling system are obvious. The cost of a 1000 hour task is illustrated in Figure 8. While the compressor micro-cooling system has a capital cost of US$650 in terms of normal capital costs, its operating costs save approximately US$10,000 over 1000 hours. This estimate is based on a domestic fuel cost of $14.33 per gallon delivered by ordinary mobile power. While mission fuel costs may vary, the benefits of RIGID's micro-cooling system are clear. In this case, a capital cost disadvantage of $650 at estimated fuel costs was eliminated in only 4 hours of field operations. (Refer to tabe 4, Micro DC Aircon, DV3220E-AC. Get A Sample Online)
Table 4, Test Conditions 120°F Ambient-120℃ Internal.
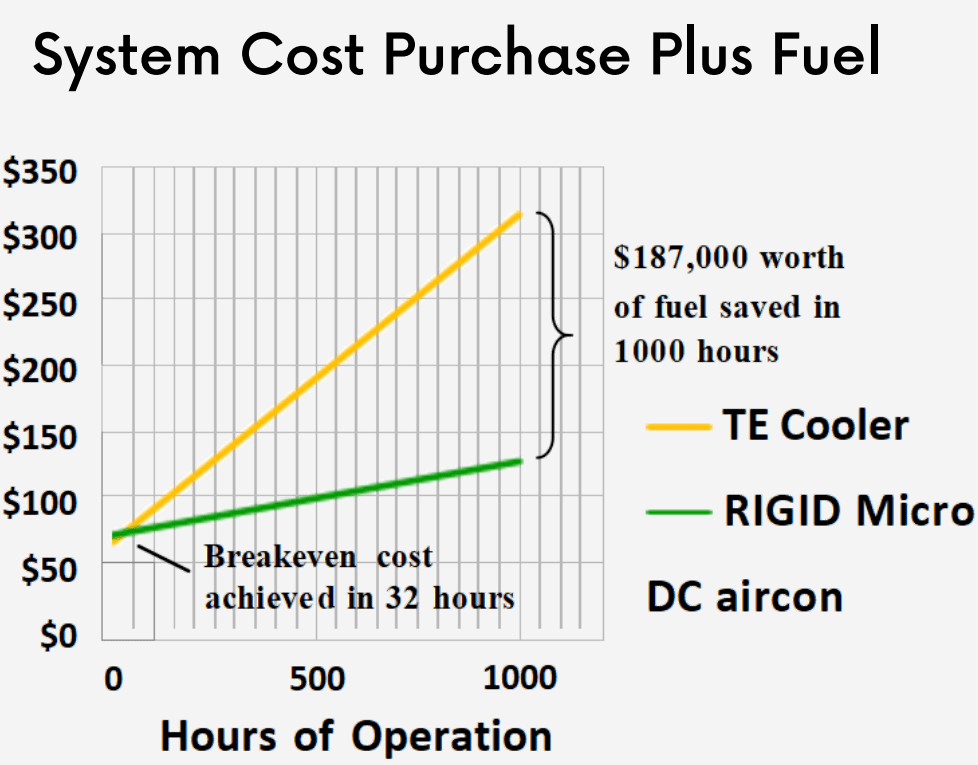
5. Conclusions
Comparative test experiments have proven that compressor vapour compression technology offers significant advantages in terms of size, weight, power consumption and also in terms of cost. Of course, the semiconductor thermoelectric structure is simpler and operates with less noise. When total costs and better cooling are taken into account, RIGID's miniature cooling systems are a better choice.
Moreover, RIGID's micro air conditioning units are both miniaturised and robust for use in harsh, high-temperature environments. the RIGID Micro DC Aircon has proven its high reliability and durability for field operation (MTBF over 100,000 hours). It uses a DC inverter micro compressor with environmentally friendly R134a or R290 for excellent cooling capacity. When exposed to harsh environments, it guarantees smooth ventilation and heat dissipation without maintenance, except for occasional cleaning of the condenser coils.
This article describes the many reasons why vapor compression refrigeration is so widely used worldwide. In addition, RIGID miniature cooling systems have excellent efficiency and effectiveness in providing cooling below ambient temperatures, especially for LBP applications. Thermoelectric coolers have a role in niche applications, they are just not suitable for long-term active mass cooling. For cooling requirements above 100 watts, compressor vapor compression cooling is the best option.
APPLICATIONS
Vapor Compressor Recirculating Chillers & Thermal Managements
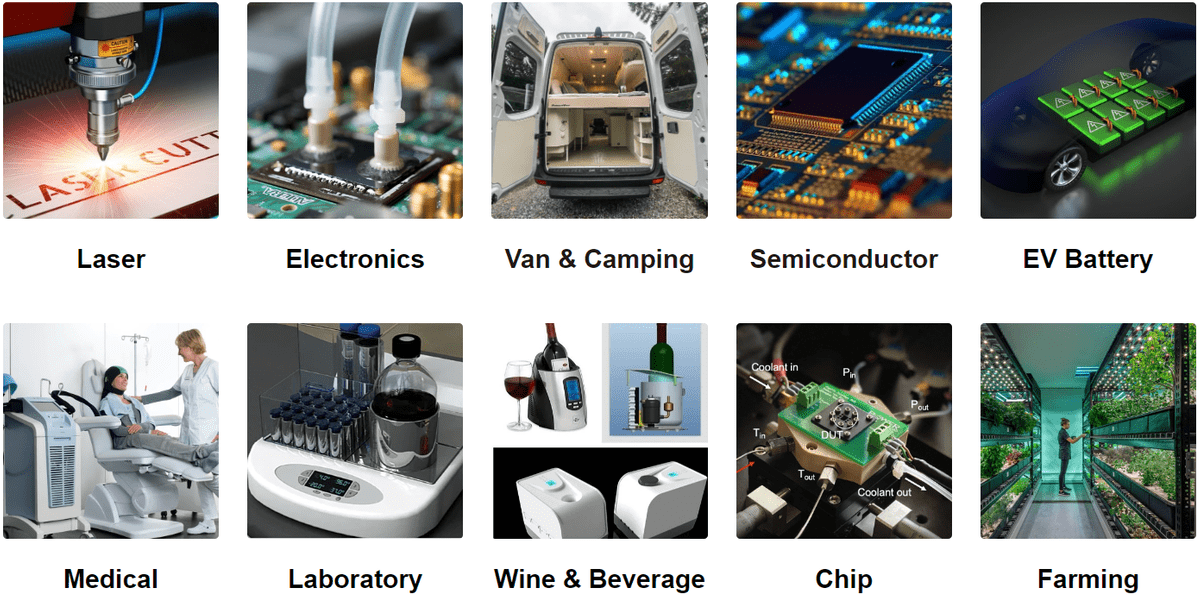