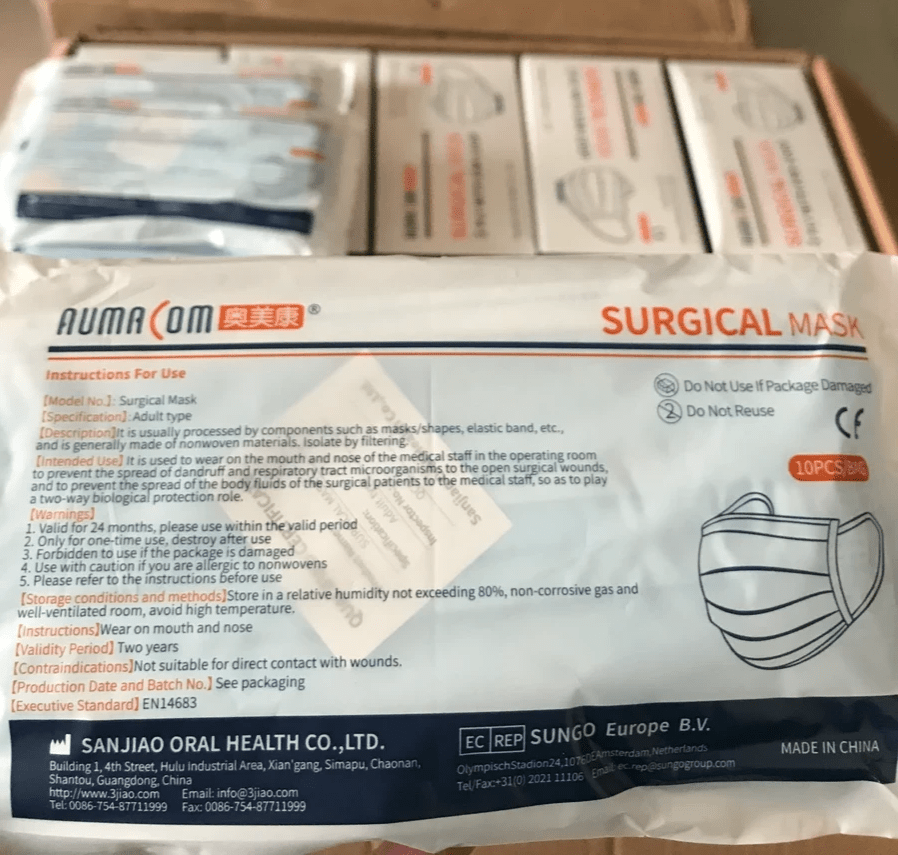
With the demand for dwindling facemasks during the coronavirus outbreak running at an all time high, many clients ask for us to collect masks. We don’t deal with epidemic products. However, RIGID is not only a business, we have our own social obligation, and we wanted to share the steps we are taking to help our employees and customers, and ensure ongoing support for our partners and clients.
Thanks to the non-stop work by the RIGID team that we were able to provide much needed help to our customers and clients. Just only 3 days, We've successfully collected 25,600pcs medical masks for our customers, helping them better prepare in this difficult time. At the same time, all projects and orders are working well to keep our business running instead of ending up in panic.
We feel this is necessary and critical to protect ourselves, our country and the world.
Here is the full nail-biting account of how we collect 25000+ masks and ship to needed customers.
8:30 p.m., March 9, 2020
Ye Bei, key account manager from RIGID Oversea dept, received a call from their VIP customer Kevin from Washington. Ye was informed that Kevin local hospital is seeking urgent help. To meet the soaring demand of masks for front-line healthcare workers and people who work in public, Kevin asked for help if RIGID can source 20000 masks and air ship to him.
Ye understood the importance of medical mask to the city, the situation in Washington is worsen. After a short call discussion with her general manager, Ye got the management’s permission and support. Ye accepted the mission without hesitation.
9:00 a.m., March 10, 2020
After finding out Kevin’s specific needs, Ye called up his team members Bao Ling and Xiao Yang, asked them to join her on this mission, and together head for the mask factory 50km away.
Upon their arrival at the factory, the factory sales guy refused Ye’s offer because of overload of orders recently. Ye never gave up and look for the factory owner.
After 3 hours negotiating, Ye finally managed to persuade him to provide us 5,600 pieces masks in advance. And then produce 20,000 pieces in 2 days for us. It had to be supported by additional workers’ manually and then it’s daily production volume of masks is 30,000 pieces per day.
Ye and her colleagues stayed focused and determined. It only took them 2 hours to finish 5,600 pieces masks counting and load to the car. Only 40mins drive, Ye came back office, call local DHL. At 14:30, the first batch of medical masks were shipped out to Washington. Under this tough situation, how did they achieve such efficiency? Ye gave credit to their “think-tank” behind the scene.
“3 colleagues from our team had been contributing their ideas in our WeChat working group throughout the night. We were not alone in this battle!” Ye said with pride.
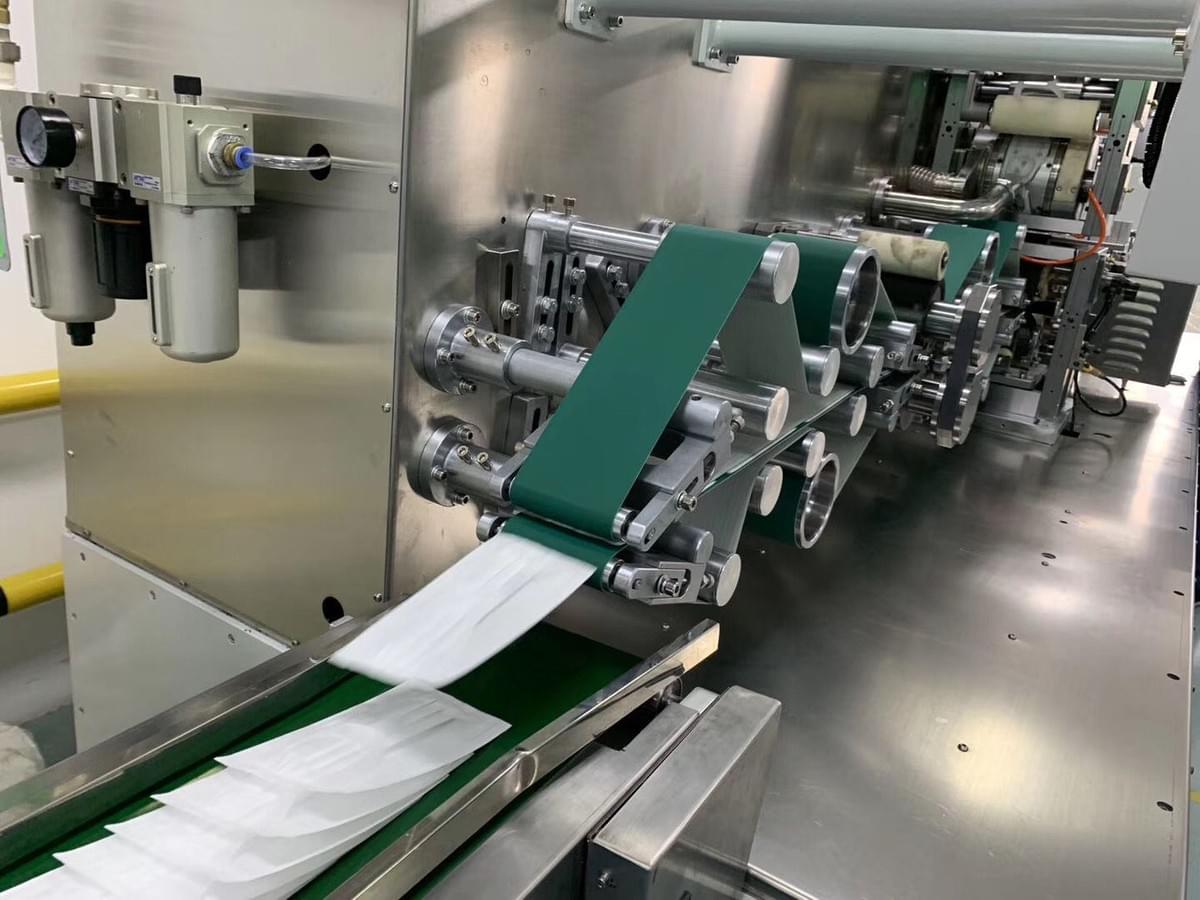
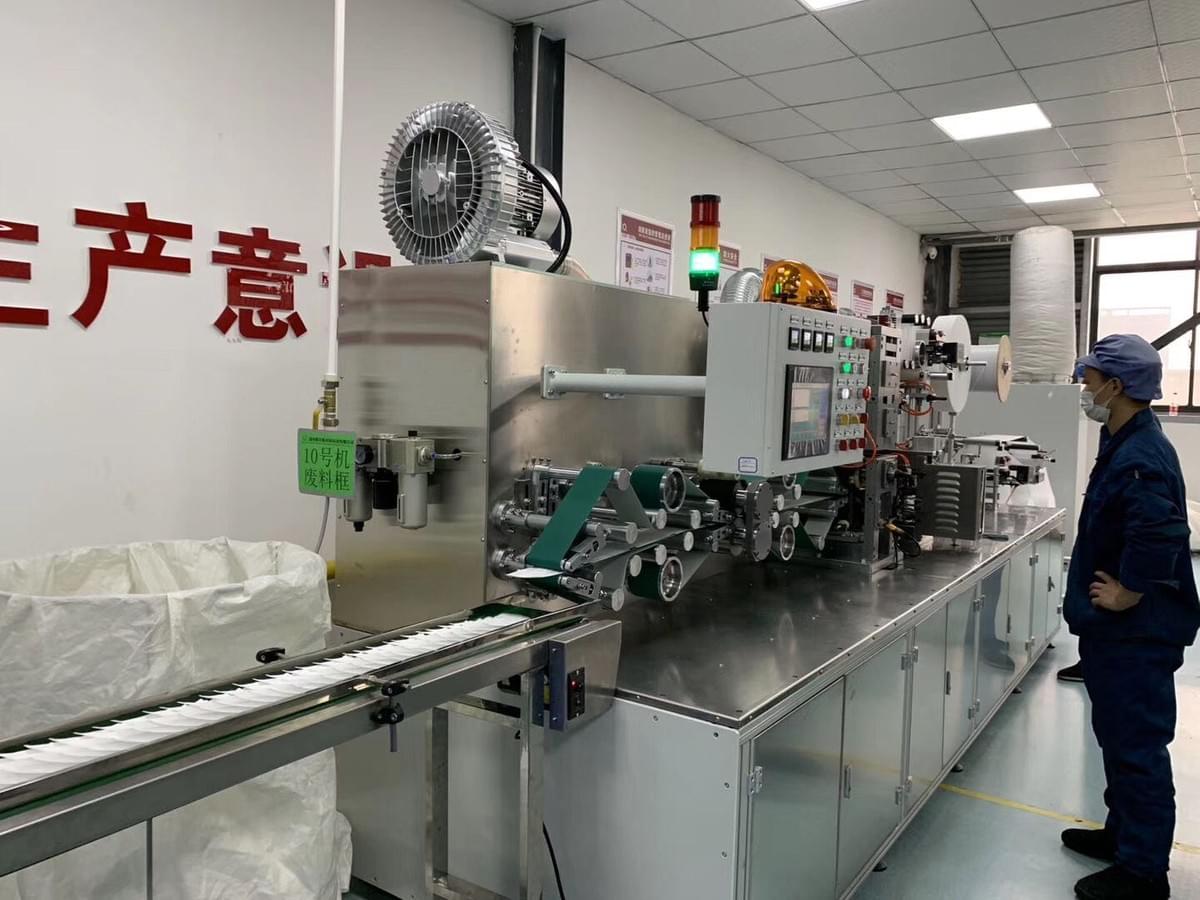
9:00 a.m., March 12, 2020
Ye and other 2 colleagues drove to the factory to follow up the mask production. Last 2 days, they called to the factory owner 3 times a day to make sure our order is on the track.
In order to avoid mistakes, Ye squatted directly in the factory production line, personally check, personally verify, to ensure that the mask is ok!
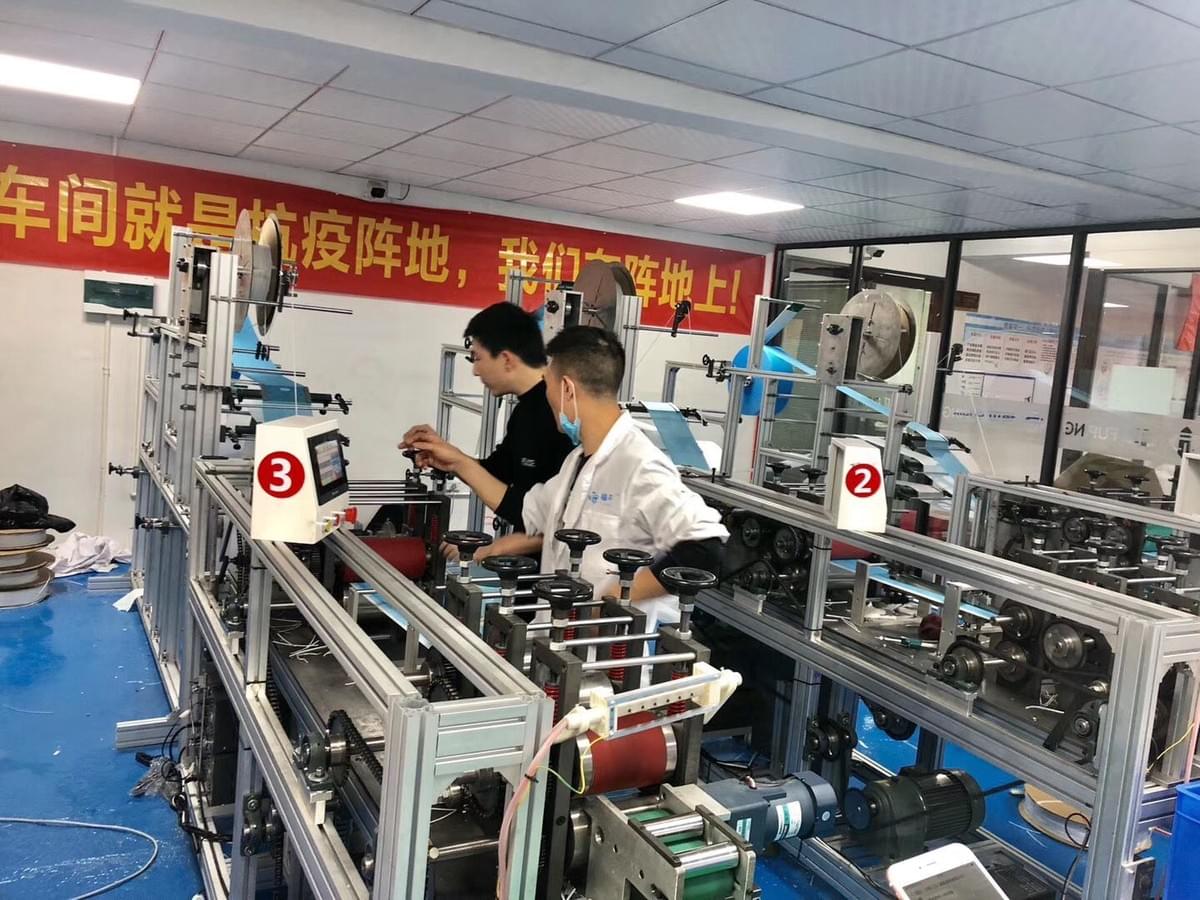
14:00 p.m., March 12, 2020
At this time, the salesman of the factory appeared and told us that the order of masks produced today was theirs and could not be given to us.Ye immediately froze up, which is impossible.YE confronted the factory clerk on the spot and finally called the factory owner.Fortunately, the boss kept his word and distributed 20,000 masks to us today.
15:30 p.m., March 12, 2020
Ye didn’t rush to leave after the call. In order to get 20,000 masks today, YE did not eat lunch and continued to wait on the production line.
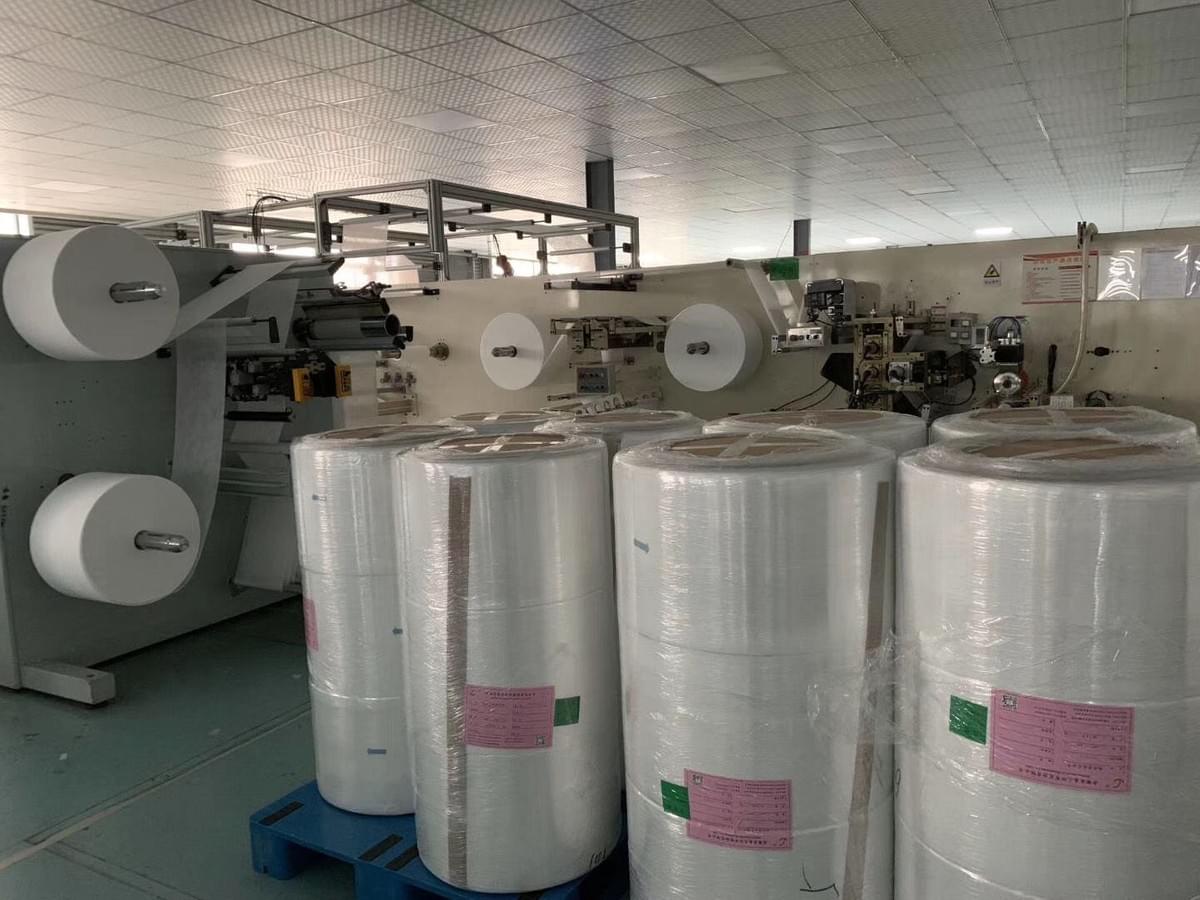
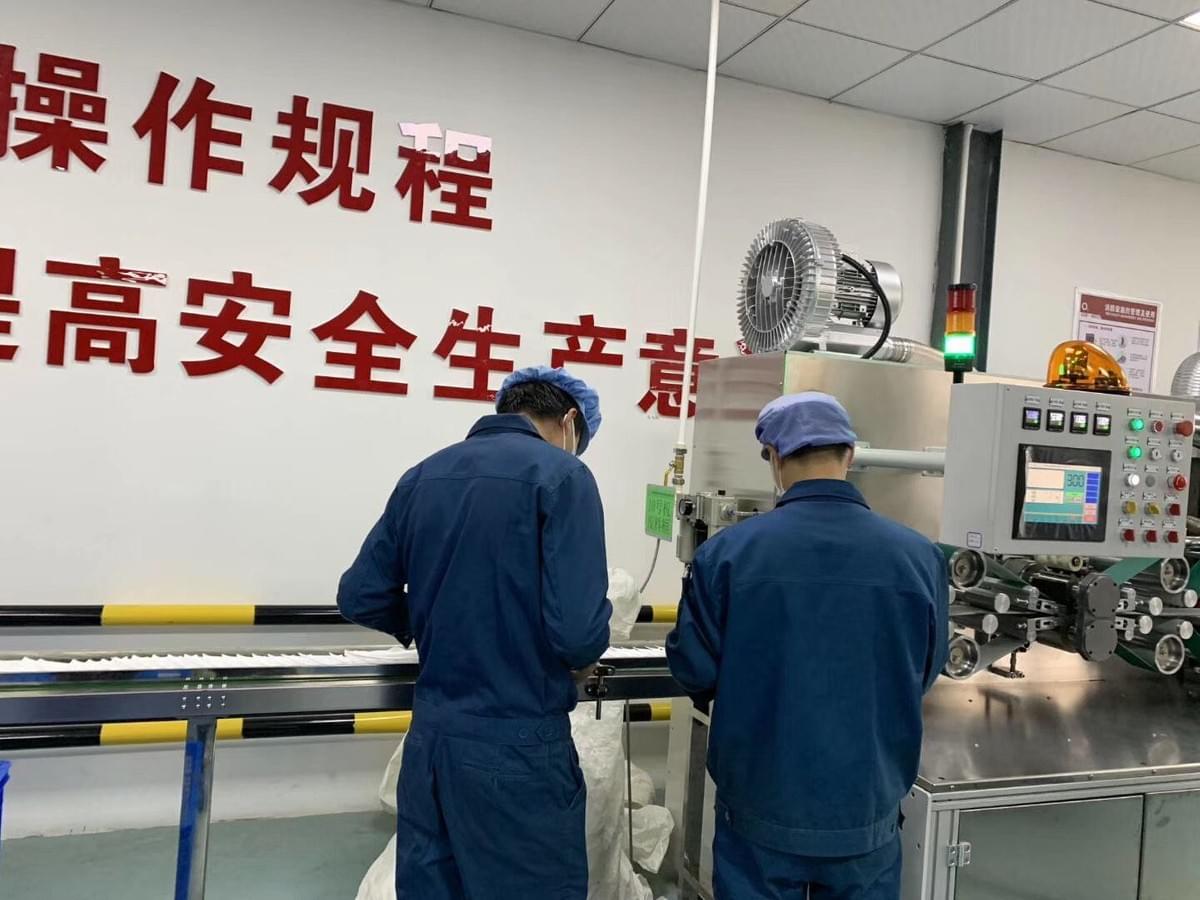
19:30 p.m., March 12, 2020
As soon as the masks came off the line, YE kept an eye on the mask packaging and then loaded the masks onto the car with two colleagues. Drive back to office without stopping.
9:20 a.m., March 13, 2020
Packed the masks, sent them to the customers and clients.
The virus impact anyone, but there's a lot we can do about it. All of us at RIGID are committed to working with our customers during this difficult time. RIGID colleagues are making positive change in our world every day. Beside the challenges, we will have to grab many opportunities to drive us to a sustainable future.
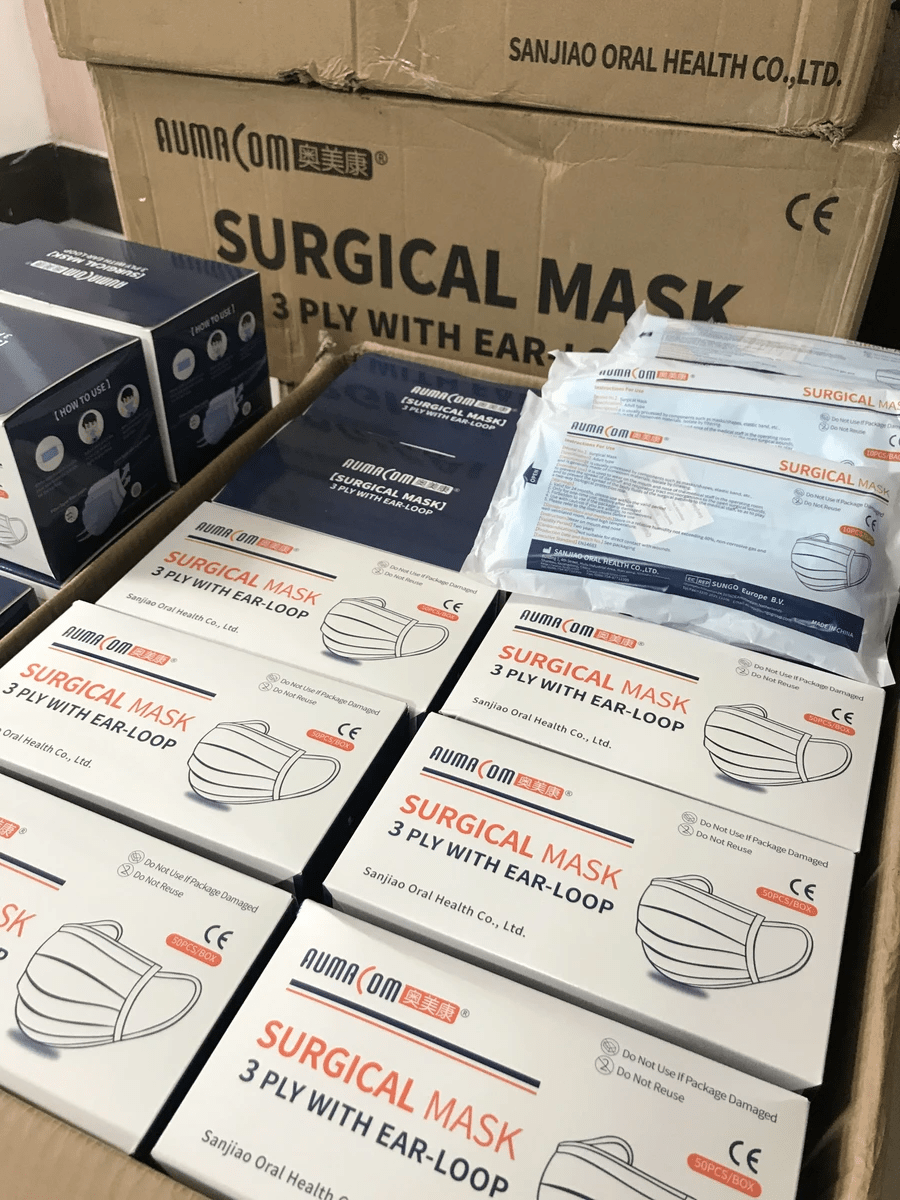
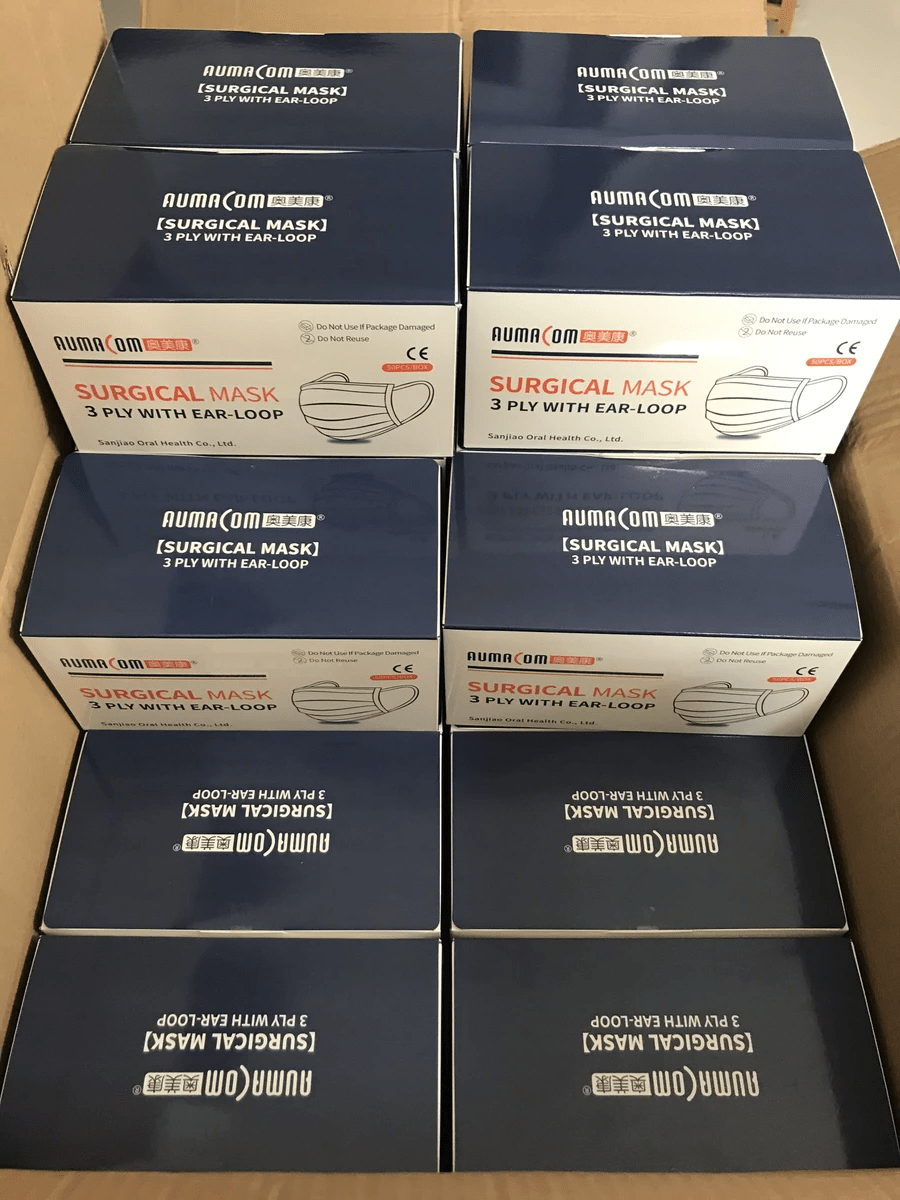
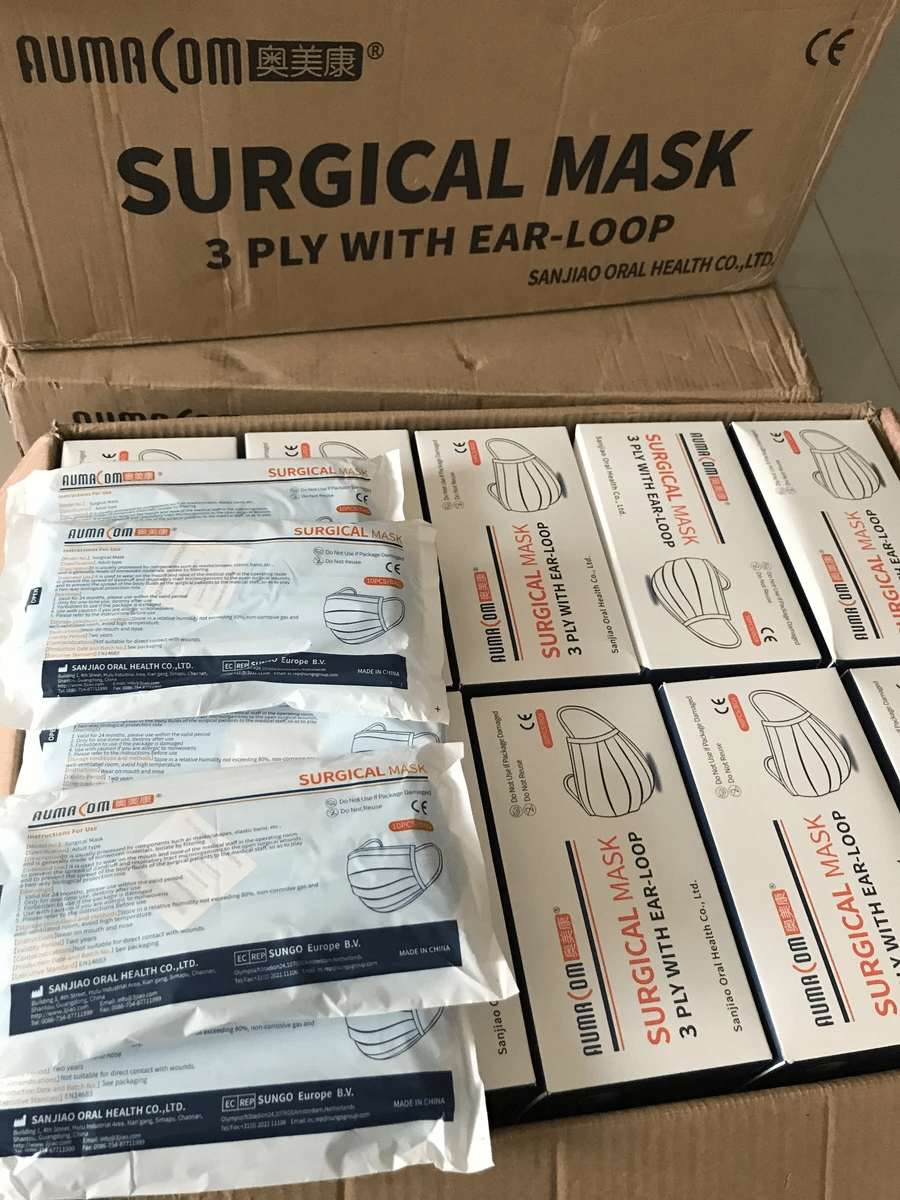
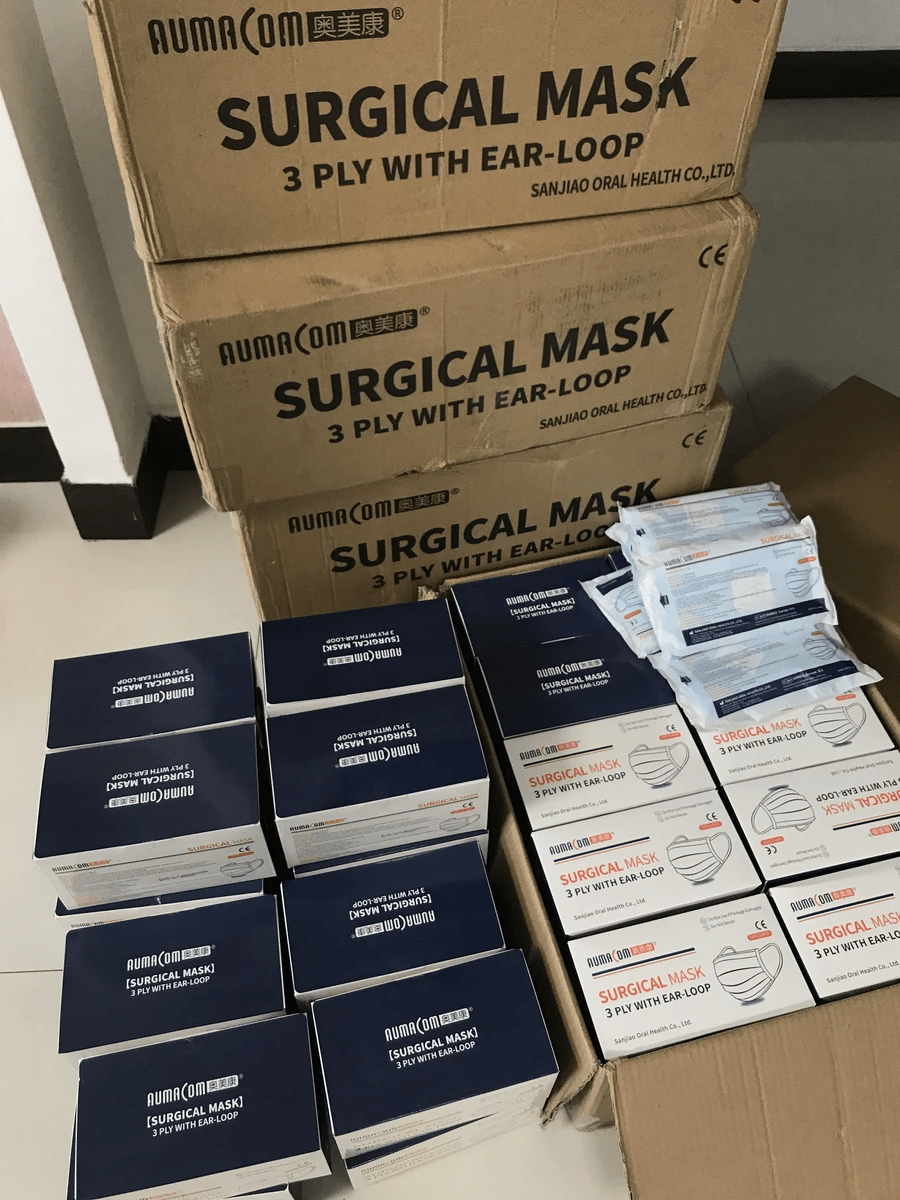